Continuous Physical Inventory
Ad-hoc Physical Inventory (Storage bin and Product specific)
Ad-hoc physical inventory can be conducted at any time during the fiscal year. This process may be executed at the level of individual storage bins or tailored to specific products.
Here are some use cases:
1. The product is damaged.
2. There is a discrepancy between ERP and EWM stock levels.
3. There is a customer complaint.
4. A product is lost or found in the bin.
Low Stock Check (storage bin specific)
The low stock check is a physical inventory process conducted during the confirmation of picking warehouse tasks (WTs).
When the picker retrieves physical stock from the designated storage bin, they can efficiently assess the available stock within the bin. During the confirmation process for the picking warehouse task, the remaining quantity can be accurately recorded. Upon confirmation, the system generates a physical inventory document, posts it, and displays the difference in the difference analyzer to post the difference in the S4.
The system evaluates the following conditions to plan the low stock check physical inventory, meaning that LSPI is activated during the creation of the warehouse task
- There are no open warehouse tasks for the storage bin.
- The relevant storage type does not allow negative quantities.
- Additionally, only a single product is present in the storage bin.
Here are the options for a low stock check:
1. Low stock check with physical inventory
2. Low stock check without physical inventory
3. Combination of options 1 and 2
Note:
- The system executes the LSPI once in a fiscal year when the storage bin goes below the defined limit.
- LSPI is activated during the creation of the warehouse task
- You can manually execute the LSPI if you have observed that the stock within the storage bin lies below the level
- The system evaluates the specified tolerance levels during the posting of the LSPI. In the event of a tolerance violation, the system does not display the remaining quantity screen on the RFUI. Instead, it records the discrepancy within the application log and calculates the product quantity by deducting the picked quantity.
*** Zero Stock check physical inventory will be done by setting the Qty to zero in the customizing settings.
Putaway Physical Inventory (Storage bin specific)
The physical inventory of a storage bin is conducted during the first putaway of the fiscal year. During this initial putaway, the warehouse employee verifies that the stock in the storage bin matches to the confirmed quantity in the Warehouse Task after the putaway is complete.
Throughout the current fiscal year, this storage bin will not undergo any additional physical inventory procedure, regardless of whether a different product is stored or if it remains empty.
For the annual physical inventory in the physical inventory year, this location then counts as inventoried so does not consider for counting.
A physical inventory putaway is created when the following conditions are met:
1. The storage bin is empty.
2. It is the first time in the fiscal year that stock is put away in the storage bin.
3. The putaway warehouse task (WT) is for a single product.
*** System does not perform the Putaway physical inventory for HU warehouse task.
When complete Handling Units (HUs) are put away, the content is not checked. Also, it is possible for one HU to contain multiple products.
Storage Bin Check
Basically, this is not a physical inventory procedure because counting is not performed in this method. Only the existence of the product is verified within the storage bin.
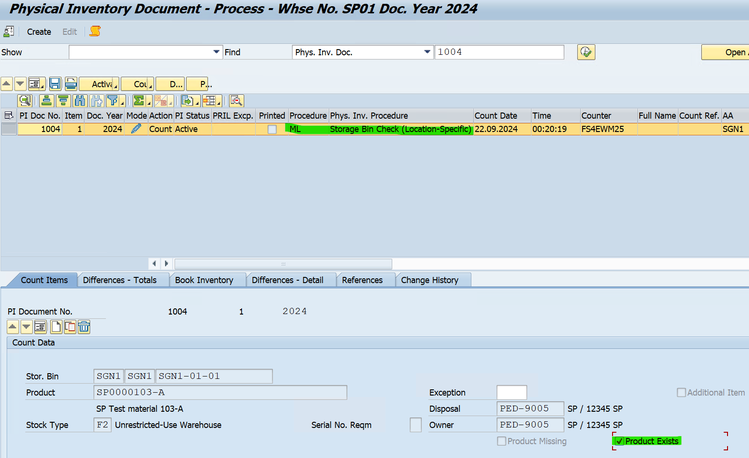
